Repensando la medición de la productividad: más allá del OEE
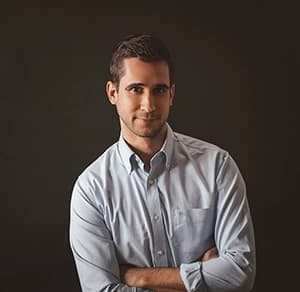
2024-04-22
Repensando la medición de la productividad: más allá del OEE
La constante búsqueda de eficiencia en las operaciones de fabricación ha llevado a los expertos a explorar métodos de medición de la productividad que trasciendan las fórmulas convencionales. El Overall Equipment Effectiveness (OEE) ha sido el estándar de oro durante años, pero, ¿es hora de innovar? En este artículo, te invitamos a descubrir un enfoque alternativo que podría revolucionar la manera en que trabaja tu fábrica.
En busca de una medición más exacta
La productividad en una fábrica va más allá de la mera cuenta de unidades producidas. Cada componente, cada producto, lleva implícito un código genético único en su proceso de fabricación, y debemos tenerlos en cuenta al realizar cualquier medición. Ignorar la variabilidad en la complejidad de los procesos de manufactura sería como tratar de medir el rendimiento de un atleta basándonos únicamente en el tiempo de las carreras que realiza, sin considerar la distancia o la dificultad del terreno.
Es imprescindible entender que no todas las unidades de producción son creadas iguales, y menos aún deben ser tratadas de manera uniforme.
Hasta ahora, el Overall Equipment Effectiveness (OEE) ha sido el método más empleado para medir esta productividad. Se trata de un indicador compuesto que mide la efectividad de un equipo o proceso manufacturero en tres dimensiones esenciales: la disponibilidad, el rendimiento y la calidad. Este indicador se ha convertido en el pilar de muchos entornos de producción por su capacidad para identificar áreas de pérdida y oportunidades de mejora.
Sin embargo, si bien el OEE ofrece una estructura útil para descomponer la eficiencia, se queda corto al enfrentarse a la diversidad y especialización de los sectores modernos. Su aplicación a gran escala o su integración en diferentes cadenas de producción a menudo resulta ser más un ejercicio de adaptación que de precisión.
Estos son algunos puntos débiles del OEE que ejemplifican por qué este sistema tiende a no ser suficiente:
- Uniformidad asumida: El OEE trata todas las operaciones como si tuvieran el mismo peso y dificultad, lo cual no es representativo de la realidad diversa y multifacética de la producción moderna.
- Rigidez en la diversificación: La métrica puede volverse menos significativa en fábricas que producen múltiples productos o que cambian las líneas de producción con frecuencia.
- Dificultades en la agregación: Al tratar de sumar o promediar el OEE para obtener una visión de toda la planta, se pueden perder detalles cruciales y sutilezas operativas. Tampoco es sencillo obtener datos de un operario en concreto.
- Falta de flexibilidad sectorial: Las fábricas modernas varían enormemente de un sector a otro. Un enfoque único para todos, como el que propone el OEE, puede no traducirse bien entre diferentes industrias con sus propias peculiaridades.
- Poca visibilidad de los procesos subyacentes: El OEE puede indicar que un proceso es ineficiente, pero no siempre clarifica el porqué. Esto puede llevar a acciones correctivas que son más bien reactivas que proactivas.
Una propuesta alternativa
Una solución innovadora para dar respuesta a las necesidades que el OEE no logra cubrir consiste en definir tiempos teóricos para cada operación, estableciendo un estándar personalizado de productividad.
Los tiempos teóricos son los estándares establecidos para la realización de una tarea específica, tomando en cuenta las condiciones ideales de trabajo y la naturaleza del proceso. Se definen basándose en estudios de tiempos y movimientos, datos históricos y benchmarking de la industria.
Al comparar el tiempo real empleado en producir una pieza con su correspondiente tiempo teórico, desbloqueamos una visión más ajustada y detallada de la eficiencia real de nuestra planta. Y el resultado es un simple porcentaje que todo el mundo entiende.
Este enfoque busca armonizar la teoría con la práctica, ajustando las expectativas a la realidad operativa individual de cada planta.
Ventajas de esta propuesta
En la búsqueda de la excelencia operativa, este sistema promete mejorar no solo el rendimiento, sino también la inteligibilidad de las métricas de productividad. Estos son los principales puntos fuertes de la medición de tiempos teóricos:
-
Calibración personalizada: En lugar de una medida única, cada línea o producto tendría su propio 'tiempo estándar ideal', lo que permitiría una evaluación más precisa y personalizada.
-
Enfoque múltiple: Esta métrica puede adaptarse tanto a procesos concretos, máquinas, áreas o personas. Cada ángulo te puede aportar información clave sobre dónde está el cuello de botella. Al ser todo un porcentaje, es sencillo de agregar.
-
Claridad en la comunicación: Un sistema más intuitivo y menos técnico facilita la comprensión en todos los niveles de la organización, lo cual es esencial para el compromiso y la implementación efectiva de estrategias de mejora.
Desafíos que presenta el nuevo sistema de medición
Si bien estas ventajas son tentadoras, también debemos ser precavidos y considerar los desafíos inherentes a la adopción de este sistema de medición, ya que nos ayudará a mitigar los riesgos y a rentabilizar al máximo sus potencialidades.
-
Establecimiento de tiempos teóricos: Definir con precisión los tiempos teóricos para cada operación puede ser una tarea compleja, que requiere un profundo entendimiento de cada aspecto del proceso productivo.
-
Dependencia de datos históricos: La efectividad de este enfoque está fuertemente anclada en la disponibilidad y calidad de los datos históricos, que son esenciales para establecer y ajustar continuamente los tiempos teóricos.
-
Requiere inversión en TI: La implementación de este sistema podría necesitar una inversión inicial en tecnología para el seguimiento y análisis de datos, ya que hacerlo en papel o Excel no es viable.
Claves para incorporar la medición por tiempos teóricos
Implementar un sistema de medición basado en tiempos teóricos implica realizar primero un estudio detallado de cada operación; por ello, este estudio debe ser riguroso y tener en cuenta la variabilidad inherente a cada proceso. Luego, estableceremos estos tiempos como nuestros benchmarks internos, contra los cuales mediremos el rendimiento real.
Es preciso tener en cuenta que este método requiere un cambio cultural y de mentalidad, pasando de un enfoque generalizado a uno personalizado. Debe promoverse entre todos los trabajadores una actitud de transparencia y apertura al cambio, donde la mejora de los tiempos teóricos se vea como un objetivo común y no como una herramienta de supervisión o sanción.
Al fin y al cabo, los beneficios de este enfoque pueden ser significativos, especialmente para las organizaciones que en la actualidad se ven limitadas o enfrentan dificultades con el modelo de OEE.
Bold Factory: un aliado en la mejora de la productividad
Imagina una plataforma que no solo proporciona las herramientas para implementar esta nueva métrica de forma automática y autodidacta, sino que también te guía a través de su integración en tu proceso de producción. Bold Factory puede ser para tu fábrica un inestimable socio tecnológico, ofreciendo una solución SaaS integrada que combina análisis avanzados con la facilidad de uso.
La personalización no es un lujo, es una necesidad en la medición de la productividad del mañana.
Si crees que ya es la hora de adoptar un sistema que refleje la complejidad y la individualidad de tus operaciones de fabricación, ponte en contacto con nosotros. Descubre por ti mismo/a cómo mejorar la forma en que vemos y medimos la productividad.